Induction Heating
Equipment & Tools for Sale & Rental
Induction Heat Treatment
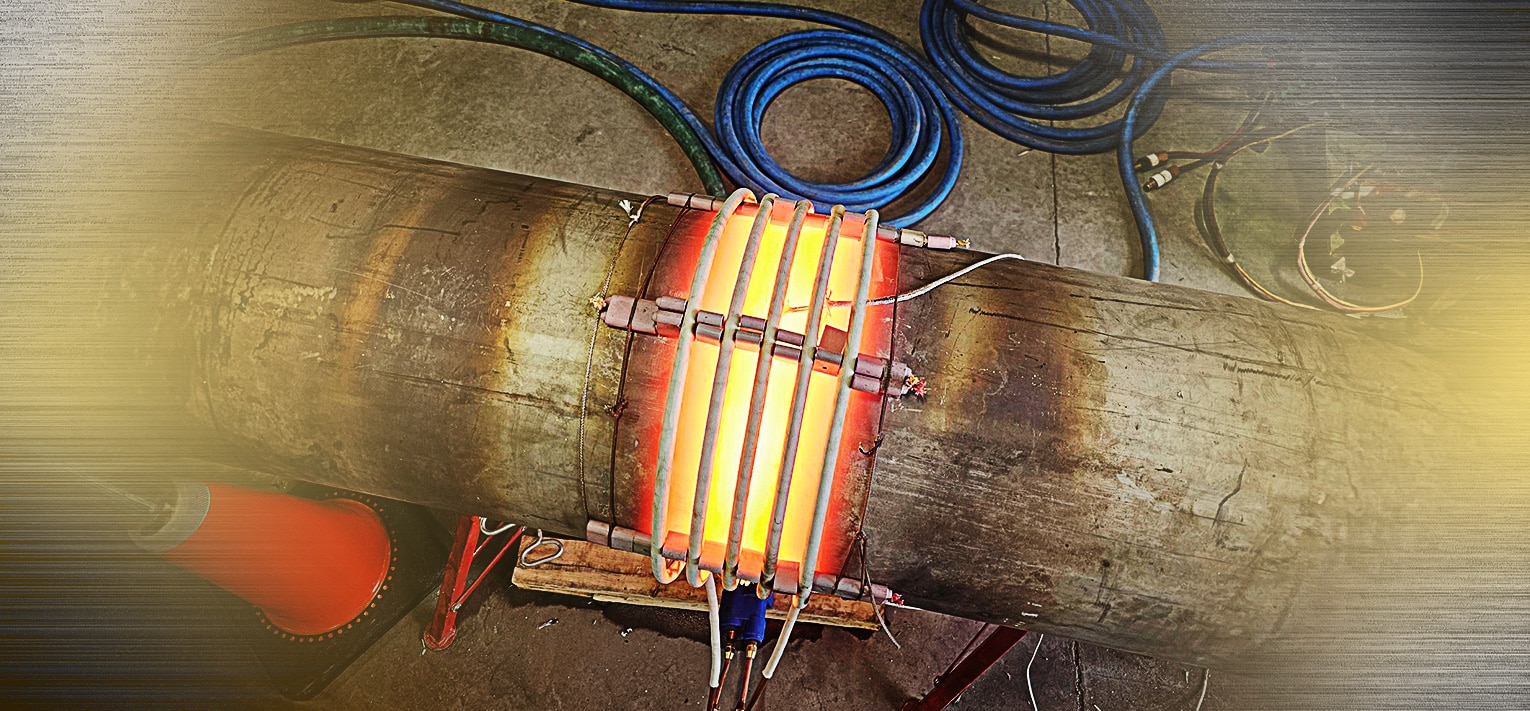
The induction heat treatment method uses Coaxial Cables to transfer power to either liquid-cooled copper braided hoses or solid copper coil wrapped around the material to be heated to create a magnetic field. As the electrical current pushes through the conductor, it creates a magnetic field. The magnetic field excites the molecules in the material, which creates heat that radiates from the center of the material outward in all directions.
For certain applications a coil can be created in a “Probe” type format. In this instance the coil is created to be placed as close to the surface of the material, to be heated, as possible, but does not actually wrap around. Examples of this are seen in Bolt Heating and Induction Brazing applications. Induction Heating Systems are great for Stud / Nut Removal, Induction Brazing, Turbine Rotor De-Stacks, Retaining Ring Removal, High Temperature Field Heat Treatment applications like Solution Annealing. It should be noted that compared to Electrical Resistance, Induction Heating Systems are far more complicated in terms of on board electronics and they required a more skilled personnel to operate them.
While induction heat treatment systems get utilized for Welding Preheat applications due to their ability to heat quickly, they have been considerably less accurately controlled than Electrical Resistance Equipment. For P-91/ P-15E materials where Minimum Preheat, Maximum Interpass, and PWHT temperature tolerances are critically important, Induction Heating Systems are less than ideal.