Combustion Heating
Equipment & Tools for Sale & Rental
Field Heat Treatment High-Velocity Combustion
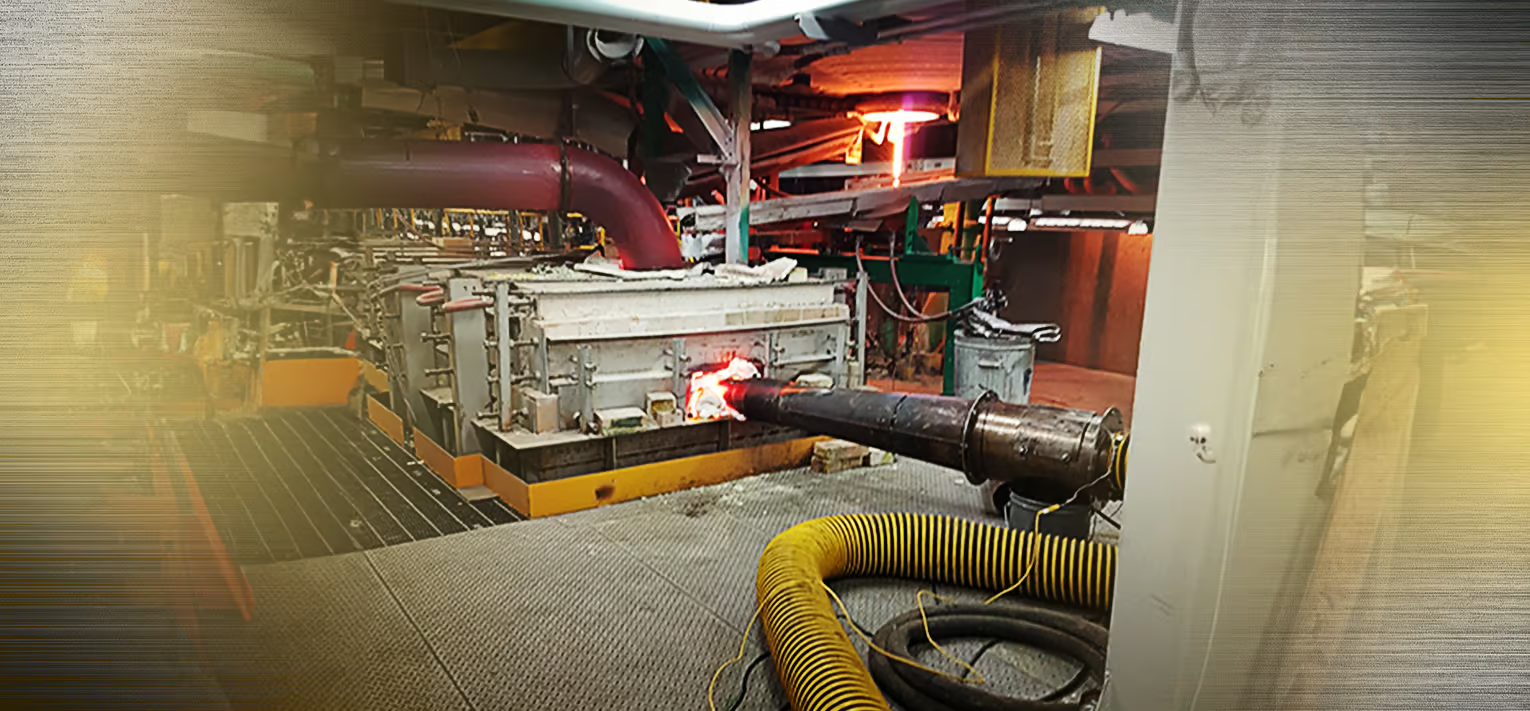
Field heat treatment high-velocity combustion systems consist of a Gas / Valve Train, High-Velocity Burner, high volume pressure Blower, and interconnecting control cabling, flexible gas hoses, and air ducts.
These field heat treatment high-velocity combustion systems are for a variety of Field Heat Treatment applications. From relatively low-temperature epoxy cures of large petrochemical storage tanks to high-temperature PWHT stress reliefs within small temporary furnaces and In-situ PWHT of large multi-story petrochemical towers to refractory dry-outs and molten metal foundry and glass furnace start-up applications.