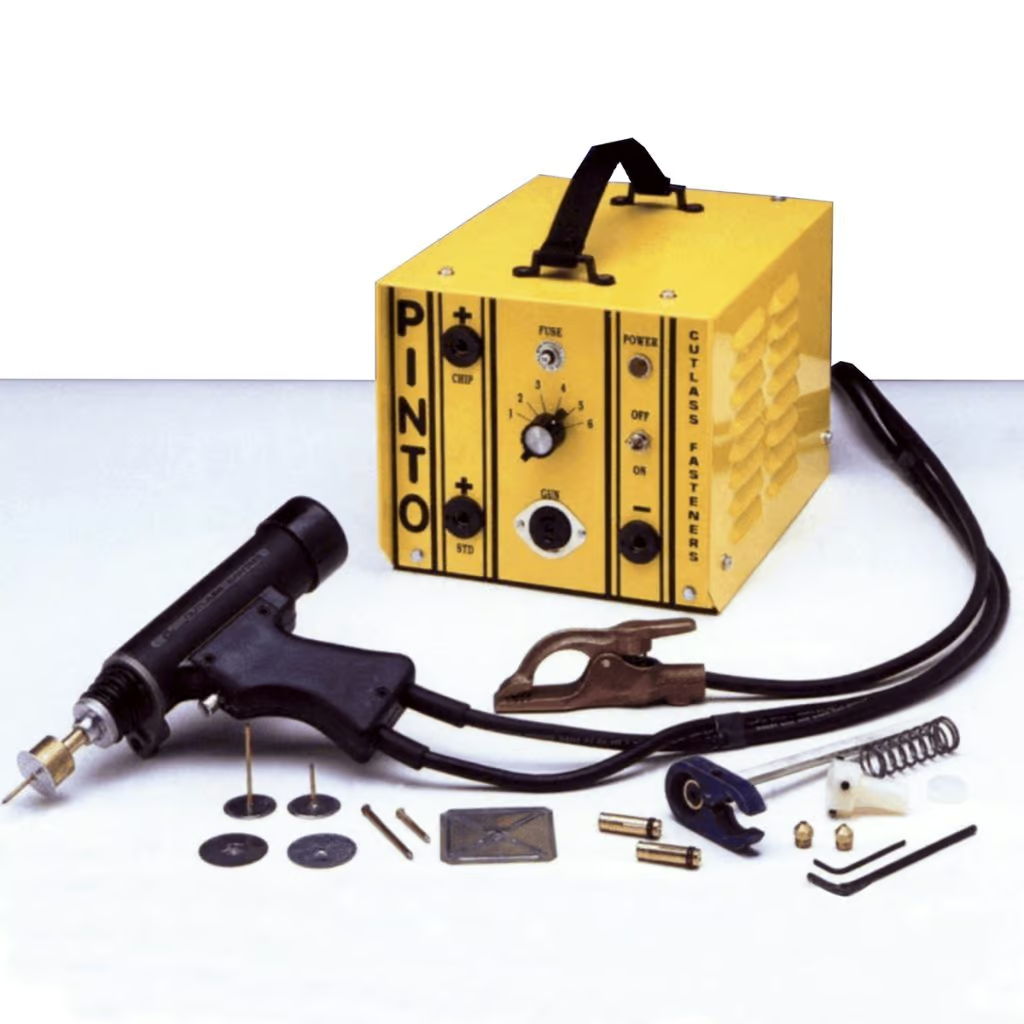
Pin Welders
99% of the Stud Welding completed for Field Heat Treating purposes is Capacitor Discharge Pin Welding. Regularly 12Ga Pins are used to fasten the Flexible Ceramic Heaters to different work pieces. 3” 12 Ga Mild Steel pins are the most used item for this purpose. Blunt Point pins have become the new industry standard for safety purposes, although some people still prefer the regular point (sharp point) pins.
The Drawn Arc Stud Welding process is used in conjunction with Insultwist Pins to secure the insulation to the interior of the furnace.